In this text, we turn to the explanation of a disjunctor, intending to inform you about what a disjunctor is and its practical applications. Make sure to stay tuned with Electrosheil to learn more about this matter than ever before. First and foremost, let’s move on to the definition of a disjunctor.
What is a Disjunctor?
A disjunctor is another key utilized in the power category. The word “Disjoncteur” is a French term that, when translated into English, leads us to the term CB or Circuit Breaker, meaning circuit breaker. Thus, we understand that it is used in the category of power circuit breakers.
A power key is a device capable of disconnecting and connecting the power circuit under specified conditions and times in a way that avoids damage and effectively controls the network. Power keys are divided into two categories: load-breakable (such as disjunctors) and non-load-breakable (such as switchgear).
A disjunctor is an operative power key that, in addition to disconnecting and connecting a circuit or line, also protects the network in case of an occurrence of a fault. This power key is load-breakable, meaning that it can disconnect the circuit when the consumer is connected, and the circuit is under load, so to speak. Depending on their design, disjunctors can control one or more parameters of an electric line. The operation command of disjunctors is issued by prime relays directly connected to a 20 kV power source.
In power systems, the separation of strong-pressure key contacts generally does not bring the line current and voltage to zero, and until these values reach zero, we will have an arc or spark. Another function of power keys is to address and resolve this issue in power systems by disconnecting strong-pressure key contacts.
Functioning of a Disjunctor
In order for a disjunctor to perform the operation of disconnecting and connecting, and return to a ready state, it is equipped with springs inside, each of which is connected to a movable shaft.
The connecting spring in the disjunctor is charged both manually and motorically, and the disconnecting spring in the disjunctor is charged by the energy released from the charged connecting spring. The control of releasing these springs is done by activating a latch through the coils of the disconnect and connect.
The coils, which receive commands for energizing, can be controlled both manually and remotely.
Disjunctors often receive the energy required for the disconnecting and connecting operation from the Spring Charge Mechanism.
This means that the energy needed for the operation of the key is stored in the springs. This mechanism simultaneously opens or closes all three or four circuit breaker terminals.
Classification of keys in terms of the operating mechanism:
The operating mechanism refers to the ability of the key to perform the disconnecting or connecting operation shortly after receiving the command. The operating mechanism in keys can be one of the following:
1. Spring Mechanism or Charged Spring Mechanism
2. Hydraulic Mechanism
3. Compressed Air or Pneumatic Mechanism
4. Manual Mechanism
5. Magnetic Mechanism
6. Motor Mechanism
All types of mechanisms are applicable to all keys, but the most commonly used mechanism is the Spring Charge Mechanism.
Spring Charge Mechanism
The Spring Charge Mechanism operates independently with two latching mechanisms. It includes a charge mechanism for manual operation and a motor-driven charge mechanism, both of which can be adjustable for both modes. Additionally, this latching mechanism has a specific type of insulating cover that protects the operator from the risk of electrical contact.
The Spring Charge Mechanism works as follows: for each connection of the key, there is a need to charge the connecting spring, and after each connection of the key, the disconnecting spring is simultaneously charged, and the key is ready to disconnect. Simultaneously with the disconnecting spring charge, by limit switches present in the disjunctor, the command to connect the connecting spring to the motor, which is responsible for the connecting spring charge, is sent. When the charge operation is completed, another set of switches issues the command to disconnect the motor. In this way, one can understand how the disconnecting and connecting springs are always ready for operation at the required moment.
Advantages of the Spring Charge Mechanism include cost-effectiveness, ease of installation and maintenance, the possibility of manual spring charging, and higher reliability. However, it also has its disadvantages. Despite these drawbacks, considering its significant advantages and the ease of installation, maintenance, and servicing, it has become prevalent. This mechanism is commonly preferred for voltage levels up to about 145 kV because it does not require a system with very high disconnecting power. Additionally, the Spring Charge Mechanism has a simple mechanism, making it the preferred choice for all manufacturers for systems at this voltage level over other systems.
Internal Structure of a Disjunctor
Disjunctors are composed of a simple switch, one end of which is connected to a coiled wire, and the other end is linked to a bimetal. This means it utilizes both magnetic and thermal functions to control and disconnect/connect the circuit.
The phase wire inside the circuit is connected to the two ends of the switch. When the switch is in the ON position, electrical current passes from the lower terminal through the coiled wire (electric magnet) and is transferred from the moving contact to the fixed contact via the movable contact, exiting through the upper terminal.
When the current exceeds a certain limit, according to the Joule effect, it generates heat and changes the shape of the bimetal. Mechanically, the bimetal makes an electrical contact that opens the protected electrical circuit. This electromechanical system is very simple and durable, but it is not precise, and its response time is relatively slow. It can be said that when the circuit is exposed to prolonged excess current, it protects the circuit and, therefore, its main function may be to protect the conductors against excessive heat, preventing a fire in the circuit. The function of the bimetal is also referred to as thermal effect.
Detection of short circuits and significant changes in current is also the responsibility of the coils inside it. The significant change in current, according to the laws of electromagnetism, creates a magnetic field around the coil wires, causing the displacement of the core and the mechanical disconnection of certain parts of the circuit. It also protects the conductors between the source and the short circuit connection.
Main Task of Magnetic Protection
The primary duty of magnetic protection is to safeguard equipment against faults such as overloads, short circuits, malfunctions, and more. Therefore, the electrical circuit must be calculated and positioned in a way that the minimum short-circuit current causes the magnetic device to trip.
A disjunctor can either have or lack thermal overload detection. Hence, there are two main types of disjunctors.
1. With overload detection, featuring curves B, C, D, and Z, with magnetic trip thresholds between 2.4 to 14 times the disjunctor’s rated current.
2. Without overload detection, featuring the MA curve, with a magnetic trip threshold between 12 to 20 times the disjunctor’s rated current.
Design of Disjunctors
The design of disjunctors is such that it can control the circuit automatically and manually under loaded network conditions and in the event of a short circuit where the current passing through the circuit may be up to ten times the rated current of the disjunctor. It is capable of disconnecting the circuit without causing any harm to it.
Because a disjunctor disconnects the circuit under load, a mechanism must be incorporated at the moment of disconnection and inside the disjunctor at the disconnection point. This mechanism should be able to discharge sparks resulting from the disconnection and reconnection of the current. To achieve this, disjunctors use oil, gas, vacuum, or other insulating mediums, and through blades, direct the sparks created towards the disconnection chamber (spark elimination chamber).
Disjunctors can be examined from two crucial perspectives:
1. Disconnection chamber
2. Operating mechanism (system for supplying kinetic energy to movable contacts)
Disconnection Chamber
The disconnection chamber, a constituent part of the disjunctor, refers to the location where the current is disconnected and reconnected through two contacts: one open and the other closed. At the moment of connecting or disconnecting these contacts, an electric arc or spark is created due to the flow of current through them. The electric arc at the moment of disconnection is greater than at the moment of connection because, during disconnection, the network is loaded, and there is voltage present in the high-voltage line. With an increase in voltage in a power system, the spark during disconnection also increases. The more powerful the consumer, the greater the magnitude of this spark. In such cases, a mechanism is required that has both high-speed and high-power disconnection or extinguishing capabilities.
The springs present in the disjunctor accelerate the disconnection action and use oil, SF6 gas, or a vacuum to eliminate sparks. Due to the relatively higher need for repair and maintenance and the potential for explosions in oil-based disjunctors, they are used less today compared to other models.
As the voltage in the line increases, the distance between the two contacts increases, and the intensity and range of the arc also increase, making it more challenging to extinguish this arc and reduce the disconnection time. In this situation, multiple disconnection chambers must be used so that the voltage between the contacts in each chamber decreases with the number of disconnection chambers. However, by doing this, the current passing through the key in all contacts and disconnection chambers reaches a balance, and no significant changes occur.
For example, if the line voltage is 400 kilovolts, and the disconnection occurs in three chambers, the voltage across each chamber is approximately 133 kilovolts, provided that the line current and load current (current passing through the disconnection chambers) are equal. All movable contacts in the disconnection chambers are controlled by a common operating mechanism. The movement of movable contacts in all disconnection chambers occurs completely simultaneously.
Operating Mechanism
The operating mechanism functions through a lever that plays the role of insulation, connected to the movable contact, transferring the energy needed for the movement of the movable contact to it through this lever. The operating mechanism initially receives commands from protective relays or control panels. Then, it provides the necessary energy for the movement of the movable contact, thereby controlling the moment of movement of the movable contact for the disconnection or connection of the control key.
If we were to supply the energy needed for contacts using equipment such as motors, it would be a straightforward task. However, every time relays give commands for the movement of contacts, the contacts need to move. Since devices like motors have a time delay to start functioning, this situation is not desirable for the system.
To address this issue and eliminate this time delay, it is natural to store the energy of the operating mechanism system in advance so that immediately after receiving commands from relays, the kinetic energy of the contacts is transferred to them. Therefore, it is necessary to predictively store this energy ready for transfer. After receiving commands from relays, at the same desired moment and without any time delay, the kinetic energy of the contacts should be transferred to them.
This stored energy is done in the form of a charged spring, pressurized oil, or compressed air. When the key is opened and closed, the spring or oil is pressurized by an electric motor or manual handle, storing some mechanical energy, which, after receiving commands from the relays, transfers the required mechanical energy for the movement of the contacts to them.
Extinguishing of Electric Arc in Disconnectors
The electric arc formed in the disconnector’s switching chamber extinguishes only when the distance between the fixed and movable contacts is sufficiently large. This distance should exceed the necessary range for the arc to develop more extensively. By gradually increasing the distance between the movable and fixed contacts, the ability to sustain the arc increases, but simultaneously, its intensity and power decrease. The continued movement and increasing separation of the movable contacts lead to a severe drop in voltage between the contacts. At this voltage level, the possibility of maintaining the arc no longer exists, and the electric arc is extinguished. The shorter the time to establish the arc, the sooner the current is interrupted by the switch.
To expedite the preparation of the disconnector’s switching chamber and enhance its dielectric properties, materials with higher dielectric properties are used in the gap between the two contacts. These materials include oil, compressed air, SF6 gas, and vacuum, where all of these, starting with vacuum and then SF6 gas, have better insulation properties compared to others. As the voltage level increases, the need for higher insulation strength arises to extinguish the electric arc in the shortest possible time. Hence, for higher voltage levels, the use of vacuum or SF6 gas becomes necessary.
Differences Between Disconnectors and Some Other Electronic Devices
Difference between Disconnectors and Sectioners
Both disconnectors and sectioners fall into the category of power switches and circuit breakers. The term “sectioner,” like “disconnector,” is a French word (Sectionneur), and its translation into English is “Sectioner” or “Isolator.” It is true that both of them belong to the family of circuit breakers, but a disconnector, as a switch disconnectable under load, has the ability to interrupt the circuit under high voltages. In other words, it can disconnect the circuit when there is voltage in the line. On the other hand, a sectioner is considered a non-disconnectable under-load switch, and it comes in various types.
It should be noted that if we incorporate a spring-charging mechanism into sectioners, they become disconnectors under load, thus increasing their circuit interruption capabilities. Since there are consumers with lower power requirements in the network that may not necessarily need a disconnector, switching operations for them can be done using sectioners.
For example, in step-down transformers on power lines that convert 20 kilovolts to 400 volts, sectioners are used to disconnect the circuit load. Another function of sectioners is to serve as isolators for disconnectors. They are placed at the input and output of disconnectors, and when necessary, the disconnector can be completely removed from the network and repaired or replaced.
In essence, sectioners are used for discharging capacitor energy and ensuring the safety of the circuit.
Capacitor energy discharge means that when the power is cut off, there is still stored electrical energy in the circuit due to the capacitor’s characteristics, which can be hazardous.
In high-voltage substations, proper interlocks are required for the correct entry or exit of equipment in the circuit and for personnel to access maintenance equipment. Interlock operations correspond to the circuit’s performance and involve key selection in the system. This type of interlock prevents unauthorized keying in the substation and ensures personnel safety when accessing the substation.
In installations that have both a disconnector and a sectioner, the sectioner cannot be used as a load disconnect switch. Each time it needs to be taken out of the circuit, the main power, or the circuit load, must first be disconnected by the disconnector. The reverse is also true when installing these two in the network; the sectioner must be installed first, and then the disconnector. This sequence must be strictly observed to avoid complications during their disconnection and reconnection to the network. When the key is disconnected, the moving contact separates from the fixed contact, and the key is disconnected. Since there is no spark quenching device in the construction of sectioners, unlike disconnectors, during disconnection, current should not flow through its contacts. If the sectioner is opened under load (when current is flowing through it), the spark created at the time of disconnecting the key has no space to extinguish and may cause the key to melt and harm the operator.
The interlock ensures that if the command to open the sectioner is inadvertently issued first, it will not operate. It preserves the circuit from malfunction and danger to the operator.
Types of Sectioners:
1. Load Disconnectable
2. Non-Load Disconnectable
3. Load Disconnectable with Removable Handle
Note: Non-Load Disconnectable sectioners are only used in substations for safety during maintenance (as isolators).
The circuit symbol for a disconnector and a sectioner is as follows: Additionally, a sectioner cannot disconnect the circuit during a fault occurrence, while a disconnector can disconnect the circuit in the event of a fault.
One of the applications of sectioners is for testing the circuit’s de-energization during maintenance, etc., as its contacts are easily visible, and by inspecting them, we can ensure that the circuit is de-energized.
Difference Between Disconnector and Fuse:
Both disconnector and fuse belong to the category of circuit breakers. However:
– A fuse operates in a very low current range, while a disconnector operates in the high-voltage current range.
– Fuses are disposable devices, and in case of overload, the fuse element quickly melts, requiring replacement. Disconnector, on the other hand, is reusable and can be reintroduced into the network automatically or manually even after use.
– The disconnector only performs the fault disconnection operation, and the additional load detection and disconnection are the responsibility of the control relays to the disconnector. The fuse detects and disconnects both additional current and overload.
– The fuse only has a bimetallic function inside it, while the disconnector has both bimetallic (thermal detection) and electromagnetic (magnetic detection using relays) functions.
– The time for disconnecting additional current in fuses is much shorter than in sectioners; fuses have a disconnecting time of about 0.002 seconds, while sectioners have a disconnecting time ranging from 0.05 to 0.1 seconds.
Difference Between Disconnector and Miniature Circuit Breaker (MCB):
The functionality of a disconnector is similar to that of a Miniature Circuit Breaker (MCB), as both use bimetallic elements for detecting overload current and relay operation for detecting short circuits. The key difference lies in the current range they operate in, where MCBs operate in low current ranges, while disconnectors operate in the high current range or power range.
Difference Between Disconnector and Breaker:
Sometimes, the term “breaker” is used interchangeably with disconnector. While associating the term breaker may be accurate in terms of being load disconnectable (in the case of a disconnector), from a more scientific perspective, breakers are generally referred to as devices working in low current and weak pressure conditions (such as automatic switches used in electrical panels or miniature circuit breakers used in home distribution networks). However, disconnectors are load disconnectable devices operating in the medium to high current and power ranges. Scientifically, using the term breaker for a disconnector is not accurate.
Difference Between Disconnector and Recloser:
As previously mentioned, a disconnector is a power switch for circuit protection and load disconnecting. In contrast, a Recloser is a type of relay responsible for commanding the reconnection of the power switch. A Recloser has the capability to disconnect and reconnect the circuit multiple times (usually three times) in case of a short circuit. If a problem occurs in the network, the Recloser disconnects and reconnects the circuit for one second. If the fault is not resolved after each reconnection, the Recloser can disconnect and reconnect the circuit up to three times. If the fault persists after three attempts, the network will remain disconnected.
Sometimes, certain temporary network faults can be resolved through a simple disconnection and reconnection. The reason for these repeated and short-term circuit interruptions is also due to the action of the recloser. Because there is no need to disconnect the entire network for temporary faults that can be easily rectified.
Types of Disconnector Structures (Based on the Type of Arc Quenching Chamber):
Disconnectors, based on the type of structure or the type of arc quenching chamber, are categorized as follows:
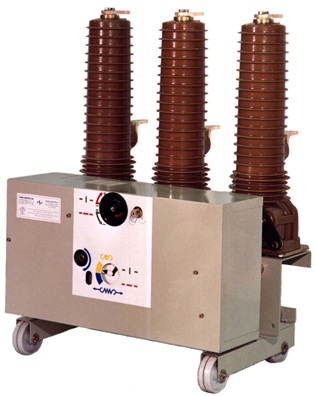
1. Disconnector with Water Arc Quenching Chamber:
This type of disconnector is very old and is no longer produced or used. Water is used as the fluid in the arc quenching chamber. The heat generated from the spark causes the water to evaporate, acting as a coolant. When the spark is extinguished, and the current reaches zero, water droplets are sprayed into the spark conduction environment. This process absorbs the free ions released from the spark, cools the spark’s path, preventing the re-ignition of the spark, and keeps it in a dormant state.
Please note that due to advancements and the availability of various disconnectors in the market, comprehensive information about all of them may not be readily accessible.
Oil Circuit Breaker (OCB or OCBS) is an acronym for Oil-filled Circuit Breakers or Oil Circuit Breaker, indicating a circuit breaker filled with oil. This type of switch is composed of a steel tank filled with oil and is operated by a strong spring. Currently, this model of disconnector is less commonly used and is being replaced by models such as gas or vacuum.
The functionality of this disconnector is similar to the water disconnector, where the oil primarily serves as an insulator, and no specific mechanism is used to extinguish the arc. As mentioned before, due to the increasing distance between contacts, the spark is automatically suppressed and extinguished because the distance is larger than the range of the generated arc. The operational mechanism of this switch is such that when the switch is disconnected and its contacts separate, a strong spark is created, leading to the vaporization of the oil around the spark. The pressure of the generated gases removes the cooling oil circulating around the arc, ultimately eliminating it. The empty space above the oil prevents an explosion during the short-circuit and spark moments by accommodating the expansion of the oil volume due to vaporization.
One advantage of this switch is its visibility, behaving like disconnectors that can be disconnected under load. However, a drawback of this type of disconnector is that it contains a considerable amount of mineral oil, possibly hundreds of liters, and ultimately involves a large volume of dead oil. In the event of a failure, it is necessary to drain this oil, posing a fire hazard. Additionally, since this oil is toxic to systems and the environment, it is crucial to control any leakage.
Air Blast Circuit Breaker
In this type of switches, the arc extinction is carried out by a blast of compressed cooling air rapidly blown between the contacts. The compressed air used for this purpose is the same air created during an explosion, stored inside a reservoir, and then compressed by a compressor. It is released through a nozzle to generate high-speed airflow. When an arc is formed between the contacts, the rapid cooling effect of the compressed air, achieved by the high-speed compressor, causes the ionized hot gases produced by the arc to be expelled. Simultaneously, as the arc is extinguished, the contacts in motion are pushed backward due to the pressure of this air, increasing the gap between the contacts, and the airflow blast valve is blocked.
These types of circuit breakers are used for indoor services in medium and high-pressure fields, as well as for applications with medium breaking capacities. Typically, they are employed in circuits with strong switching requirements in open-air spaces for voltages up to 15 kilovolts and breaking capacities of 2500 mega-volt-amperes, for a 220-kilovolt line.
Advantages and Desirable Features of Air Blast Circuit Breakers
1. High-Speed Performance: The extremely rapid interval between the formation of the arc and the separation of contacts necessitates the continuous use of these circuit breakers in large interconnected circuits to maintain system stability.
2. Suitable for Frequent Use and Replacement: The absence of oil and minimal contact wear allows for frequent replacement. However, if a circuit switch is planned for frequent switching, adequate air supply must be considered.
3. Easy Maintenance: Due to the planned frequent switching and the absence of oil, maintenance is straightforward.
4. Optimal Size: The high-speed air blast results in a rapid increase in contact resistance. With even a minimal gap, the electric arc is quickly extinguished, eliminating the need for a large space for contact movement and ultimately reducing the size compared to oil-filled types.
Air blast circuit breakers are classified into three types based on the direction of the compressed explosion around the contacts: Cross Blast Air Circuit Breaker, Axial Blow Circuit Breaker, and Radial Blast.
However, these circuit breakers have certain drawbacks:
1. Continuous Availability of Compressed Air: Properly pressurized compressed air must always be available. This may lead to the installation of larger compressors or the installation of multiple compressors, ultimately increasing their size.
2. Maintenance Costs: Due to the maintenance required to prevent air leakage, particularly at low voltages, the costs may be higher compared to gas and oil circuit breakers.
3. Noise Generation: A significant drawback is the loud noise generated during air blowing, prompting the need for soundproofing when these circuit breakers are used near residential areas.
Gas Circuit Breaker (GCB)
The term GCB stands for Gas Circuit Breaker, indicating a circuit breaker filled with gas. Typically, the gas used in these types of circuit breakers is SF6 (Sulfur Hexafluoride), also known as sulfur hexafluoride. Due to the ease of maintenance compared to oil-based switches, minimal space requirements, low noise levels compared to air-based switches, and extremely fast arc extinction, this type of circuit breaker is commonly used in various industries, residential areas, and primary substations in cities.
SF6 gas was first used as an insulating material in circuit breakers in the 1940s. Due to its characteristics, such as high stability, lack of odor, tastelessness, and non-toxicity, as well as its ability to quickly regain insulating properties within 3 microseconds after the formation of an arc (compared to air circuit breakers, which take 8 microseconds), SF6 gas has become widely utilized. Currently, these gas circuit breakers are extensively employed, especially in substations with voltages of 63 kilovolts and above, according to the standards of the Ministry of Energy. They are considered the prominent choice, as other circuit breakers lack the qualitative competitiveness of this type.
Gas circuit breakers are often connected between a generator and a step-up transformer, serving as a reliable, fast, and economical method for system protection. These circuit breakers have a nominal current ranging from 4 kiloamperes to 40 kiloamperes, and a breaking capacity ranging from 50 kiloamperes to 275 kiloamperes.
It is important to note that SF6 gas is recognized as the most potent greenhouse gas, having a global warming potential 23,900 times higher than carbon dioxide (CO2).
Key Advantages and Superior Characteristics of Gas Circuit Breakers (GCB):
– This gas is comparatively calmer than air, and during its operation, no hot gas is discharged.
– Unlike air circuit breakers, it does not require a compressor to maintain its pressure.
– The higher dielectric resistance of the gas compared to air allows it to quickly extinguish the electric arc with less contact spacing (even compared to air circuit breakers). Ultimately, it occupies less space and is lighter in structure compared to air circuit breakers.
– Its operational mechanism is simpler, and due to the absence of insulating materials like oil, it requires less maintenance and repairs.
– The absence of insulating materials such as oil eliminates the risk of fire hazards.
– SF6 gas is odorless, colorless, non-toxic, and non-flammable.
– Chemically stable, with minimal tendency for chemical reactions, it retains its nature even during arcing.
– Maintains its properties at high temperatures.
– Capable of absorbing free electrons, creating negative ions to resist arc formation.
– Due to the short distance between contacts in this switch, its opening time is approximately 35 milliseconds.
Disadvantages of these types of circuit breakers include:
1. When the electric arc is extinguished by SF6 gas, small amounts of gases of low magnitude are produced, some of which can be harmful and irritating to the eyes and respiratory system. During routine inspections, maintenance, and repairs, this can raise concerns for operators.
2. The molecular weight of SF6 gas is 146/0.06, making it heavier than air and slower to displace. Therefore, precautions must be taken to ensure that oxygen does not enter the gas compartment during the opening of the breaker.
3. In extremely low temperatures, unlike air, this gas turns into a liquid, reducing its ability to interrupt fault currents. In such cases, heaters must be equipped to maintain its effectiveness.
4. Due to gas leakage over time, the pressure inside the compartment may decrease, affecting its insulating properties. To prevent this, sensors are installed to detect a decrease in gas pressure, allowing the injection of SF6 gas into the switch.
5. The transient voltage generated in this circuit has a steep slope, requiring the use of capacitors in these systems to reduce its gradient.
Components of an SF6 switch include:
– SF6 gas compartment
– Pressure indicator for monitoring gas pressure
– Input and output terminals of the switch
– Breaker disconnect button
– Breaker connect button
– Status indicator for the on/off position of the breaker
– Status indicator for the charging of the spring mechanism
– Manual spring charging lever
– Counter for the number of breaker operations
– Lock to prevent tampering with the breaker by others
– High-pressure fuse for protection against excessive short-circuit currents.
The Vacuum Circuit Breaker (VCB) is an essential switch with its contacts enclosed in a vacuum chamber, free from any gas, air, oil, or water. The design of this type of switch must be precise to prevent an increase in pressure due to external factors. These power switches are completely waterproof and produce no noise (even less than gas counterparts), making them essentially silent. This characteristic makes them widely used in high-traffic work environments such as subways, railways, industrial factories, and more.
This equipment serves as a key component in both medium and high-voltage circuit breakers. Vacuum interrupters can also be utilized as load-breaking switches.
Over time, advancements have been made in vacuum interrupters, and due to their numerous advantages, such as exceptionally low noise, they find extensive use in power transmission systems, power generation units, and power distribution systems for railways, arc furnace applications, and industrial plants.
The high degree of waterproofing in vacuum interrupters results in minimal sound production. These vacuum circuit breakers are primarily employed in power substations and subsequently for end-users in the power grid. The utmost precision is crucial in the design of these switches to ensure that the vacuum pressure within them remains constant.
The contacts within it must be made of materials that possess high breaking capacity, excellent electrical conductivity, low thermal conductivity, high heat capacity, and the ability to emit electrons even at low levels. They should be resistant to electrical erosion and inherently have high breaking voltage.
They should resist welding and be made of alloys that withstand welding.
The current-carrying capacity of their breaking current should be low.
The contacts in this switch, like in other switches, remain closed under normal and fault-free operating conditions. In case of a fault in any part of the system, the contacts separate. In a perfect vacuum, where there is no charge carrier or ionized substance, it is expected that when the contacts open, no arc or electric arc is created. However, in practice, due to factors such as the brief evaporation of materials from the contacts, the environment becomes charged with carriers, leading to the establishment of an electric arc. As the arc spreads in the vacuum, electrons, metallic vapors, and ions produced by the arc quickly accumulate on the surface of the breaker contacts. They rapidly cool down, improving the dielectric strength. As a result, the electric arc, or spark, created is quickly extinguished, preventing the re-establishment of the arc.
History of the Emergence of Vacuum Circuit Breakers
Some vacuum circuit breakers were patented in the 19th century. In 1926, a group in California studied vacuum switchgear, examining the fundamental aspects of arc interruption. That same year, they predicted their commercial application. In 1927, General Electric began the commercial development of vacuum circuit breakers by acquiring the patent rights.
After 1970, vacuum switches gradually replaced low-oil switches. Over time, the production and development of these circuit breakers increased, and now they are manufactured in various models and for different applications, benefiting from numerous advantages.
Advantages of Vacuum Circuit Breakers
1. Minimal need for excessive maintenance compared to other circuit breakers.
2. No risk of fire due to the absence of insulating materials like oil.
3. Extremely high waterproofing, producing no noise, and being free of environmental pollution.
4. Vacuum has a higher dielectric strength than other insulating gases (eight times that of air and four times that of SF6). Additionally, the energy dissipation and axial length of the electric arc in a vacuum are one-fourth of that in gas and one-tenth of that in oil. This results in the quick extinguishing of the arc with a short contact separation distance, demonstrating very high arc extinction speed. Therefore, their reliability is higher compared to other types of circuit breakers, and vacuum switchboards have minimal contact wear (due to the high arc extinction speed in a vacuum).
The structure of vacuum circuit breakers is designed in a way that they can operate correctly even with low pressure and power, using the minimum possible amount of energy for their operation compared to other types of switches. Due to their numerous advantages, they find widespread applications in a wide range of voltage and current levels.
1. Efficiency with Low Power:
– Vacuum circuit breakers can function properly even with low pressure and minimal energy compared to other types of switches.
2. Wide Range of Applications:
– Due to their significant advantages, vacuum circuit breakers have a broad range of applications in high-voltage and high-current scenarios.
3. Compact Design:
– The high speed of arc extinction and the high dielectric strength of vacuum circuit breakers result in minimal contact movement space, making these switches compact in size.
4. Lower Heating Potential:
– The heating potential of vacuum circuit breakers is much lower than that of SF6 gas.
5. High Number of Operations:
– The number of times a circuit can be opened and closed using vacuum circuit breakers is four times higher than similar gas circuit breakers (approximately 100 operations for vacuum circuit breakers compared to 25-30 for gas circuit breakers).
6. Simplicity in Operation:
– The simple spring mechanism is sufficient for the operation of vacuum circuit breakers, as they do not require complex mechanisms like pneumatic (air) or hydraulic (oil) systems. This simplicity contributes to a longer lifespan for these switches.
7. Absence of Voltage Gradient Issues:
– Unlike SF6 circuit breakers that use capacitors to reduce the voltage gradient in the system, vacuum circuit breakers do not face this issue.
8. Compact Electrical Panels:
– Electrical panels constructed with vacuum circuit breakers are smaller in size and more compact compared to panels with gas or air switches.
9. Environmental Compatibility:
– Vacuum circuit breakers are more environmentally friendly compared to SF6 gas.
Disadvantages of Vacuum Circuit Breakers:
1. Surge Arrester Requirement:
– When using vacuum circuit breakers to discharge excess voltages, it is necessary to use a Surge Arrester (also known as lightning arrester). This is in contrast to other types of circuit breakers, where the greater distance between their contacts results in significantly lower additional voltages, eliminating the need for surge arresters.
2. Limited Repairability:
– While vacuum circuit breakers have a long lifespan, in case of failure, they must be replaced and are not easily repairable.
3. Self-Healing Property:
– Vacuum circuit breakers possess self-healing characteristics, making them excellent for interrupting high-frequency currents. The arc or spark generated due to contact separation is extinguished in the vacuum, providing efficient current interruption.
Arc Extinction in Vacuum Circuit Breakers:
The extinguishing of the arc in vacuum circuit breakers depends on vapor pressure and the electron emission properties of the contact material. The arc extinction surface is also influenced by thermal conductivity. Lower thermal conductivity results in a lower arc extinction surface.
– The ability to extinguish the arc is influenced by the vapor pressure of the contact material. Selecting a material that provides sufficient metal vapor allows the elimination of the arc with very low additional current. However, this practice is rarely performed in practice due to its negative impact on dielectric resistance.
– Vacuum has high dielectric resistance. The dielectric resistance quickly establishes during zero current, and the arc is rapidly extinguished. This phenomenon is attributed to the presence of metal vapor, which rapidly diffuses between the contacts due to the absence of gas molecules.
Extinguishing Spark or Arc in Vacuum Circuit Breakers
The extinguishing of an arc in a vacuum circuit breaker is influenced by vapor pressure and the electron emission characteristics of the contact material. The arc extinction surface is also affected by thermal conductivity. The lower the thermal conductivity, the lower the arc extinction surface.
By selecting a material that provides sufficient metal vapor, it is possible to extinguish the arc with very low additional current. However, this practice is rarely performed in reality due to its negative impact on dielectric resistance.
High-vacuum conditions result in very high dielectric resistance. During zero current, the dielectric resistance quickly establishes, causing the arc to extinguish rapidly. This phenomenon is attributed to the presence of metal vapor, which rapidly diffuses between the contacts due to the absence of gas molecules.
Minimum Oil Circuit Breakers
To achieve greater cost savings in the production costs of oil circuit breakers, semi-oil circuit breakers are designed and manufactured today. These breakers consume approximately half the oil of traditional oil circuit breakers, leading to more cost-effective solutions.
Oil-Free Circuit Breakers
In these circuit breakers, oil is not used as insulation between the contacts and serves only to cool the electric arc. Therefore, the amount of oil used in these types of breakers is much less than that in oil circuit breakers. The arc chamber in these breakers is also very compact, so that with the initiation of an arc, the oil quickly heats up, and the vapor pressure generated from it rises significantly. As a result, the breaker can easily extinguish the arc in a short period. Some of these breakers are equipped with an oil circulation pump to extinguish arcs related to small currents.
Today, the use of these power breakers has decreased due to the explosion risk associated with the oil reservoir.
The nominal current of these breakers is as follows:
630, 800, 1250, 1600, 2000, 2500, and 3150 Amperes
And their breaking capacities are in the following ranges:
12, 20, 25, 31.5, and 40 kiloamperes
In cases where the breaking capacity needs to exceed the maximum capacity of a single circuit breaker, a series connection of multiple breakers is employed to access the desired voltage.
The specifications of medium-voltage circuit breakers are provided by international standards such as IEC 62271.
Selecting Factors for Circuit Breakers
Circuit breakers are categorized based on various characteristics that can serve as factors for selecting a suitable circuit breaker for a circuit. These characteristics, in terms of circuit specifications, include:
1. Nominal Voltage: The permissible voltage for normal circuit operation.
2. Maximum Nominal Voltage: The maximum allowable voltage for normal circuit operation.
3. Nominal Frequency: The permissible frequency for normal circuit operation.
4. Nominal Current: The allowable current for normal circuit operation.
5. Short-Circuit Current Breaking Capacity
6. Short-Circuit Current Making Capacity
7. Insulation Level
8. Transient Recovery Voltage (TRV): The voltage appearing across the contacts after interruption, before reaching their nominal values.
9. Timing Sequence for Opening and Closing
10. Opening Time
11. Closing Time
Peripheral components of a circuit breaker include:
– Structure
– Arc Chute
– High-Pressure Terminals
– Gas Pressure Measurement Device
– Control Panel
– Supporting Bases
The structure or physical construction of circuit breakers is crucial in determining their overall performance.
Galvanized Coating in High-Voltage Electrical Equipment
Many switches and devices used in high-voltage electrical installations are equipped with galvanized coatings and are installed on metal structures. When making a purchase, attention should be paid to the dimensions of the switch, welding points, and its configuration. Often, many accessories and equipment are delivered alongside the switch by manufacturers.
Insulators
Insulation between line phases and poles connected to the ground is crucial to withstand voltages. The insulator has a very high resistance, serving to insulate between conductors and between conductors and the ground. Its resistance must be sufficient to prevent electrical conductivity under adverse weather conditions such as rain, thunder, and humidity.
Insulators are made from various materials, including porcelain, plastic, and glass. The chosen material should withstand the weight of conductors for supporting aerial cables on poles and structures under harsh environmental conditions, such as the presence of ice on the wires, and should endure the maximum mechanical forces.
Additionally, there are various types of insulators based on their application and voltage level in the network, including:
1. Pin Insulators: Used in distribution lines.
2. Suspension Insulators: Employed in high-voltage transmission lines.
3. Strain Insulators: Installed at points where the conductor changes direction.
These insulators play a critical role in maintaining the integrity and safety of electrical systems in different environmental conditions.
Types of Insulators:
1. Wheel Insulator:
– Description: Insulator with a wheel-like design.
2. Saucer Insulator:
– Description: Insulator with a saucer-shaped structure.
3. Standard Saucer Insulator:
– Description: Saucer-shaped insulator designed according to standard specifications.
4. Anti-Fog Saucer Insulator:
– Description: Saucer-shaped insulator designed to resist fog.
5. Aerodynamic Saucer Insulators:
– Description: Saucer-shaped insulators designed with aerodynamic features.
6. Pin Insulator:
– Description: Insulator with a pin-like structure.
7. Bell-Shaped Insulator:
– Description: Insulator with a bell-shaped design.
8. Integral Insulators:
– Description: Insulators with a unified structure.
9. Bushing Insulators:
– Description: Insulators used in bushings.
High-Pressure Terminals:
These terminals serve as connection points in the network and provide a path for current flow and short-circuit connections. They are usually made of aluminum alloy to withstand the necessary forces.
Gas Pressure Measurement Device:
This device includes an alarm for measuring the gas pressure in the insulator. It features two contacts, both measuring gas density. The first contact indicates a reduction in gas density to a level where switch-off is still possible, while the second contact indicates a hazardous situation where switch-off is not feasible.
Control Panel:
Used as an interface to connect protective equipment in the switch with control equipment in the control room. It is typically made of sheet steel with a furnace gray color to meet IP54 protection requirements and withstand dust, rain, and other environmental factors.
Support Bases:
Designed to accommodate the placement of the switch.
We appreciate your company throughout this article. Make sure to check out our other articles as well. For the purchase of a disconnector, you can seek assistance from electrical experts.