In recent decades, with the increasing use of energy and advances in technology, energy consumption in electrical systems has been challenged. One of the key aspects of optimizing energy consumption and improving the performance of electrical systems is power factor correction. Power factor correction capacitors have been recognized as key tools that can improve power factor and increase the efficiency of electrical systems. These capacitors, by absorbing reactive power and correcting the ratio of active power to reactive power (power factor), help reduce energy losses, increase system efficiency, and reduce operational costs.
In this article, we will compare dry power factor correction capacitors with oil-filled capacitors and examine the advantages and disadvantages of each. This comparison not only addresses the performance and efficiency of these capacitors but also considers their effects on the performance of electrical systems. By reading this article, readers will be able to make better decisions regarding the selection and use of power factor
correction capacitors in their electrical systems.
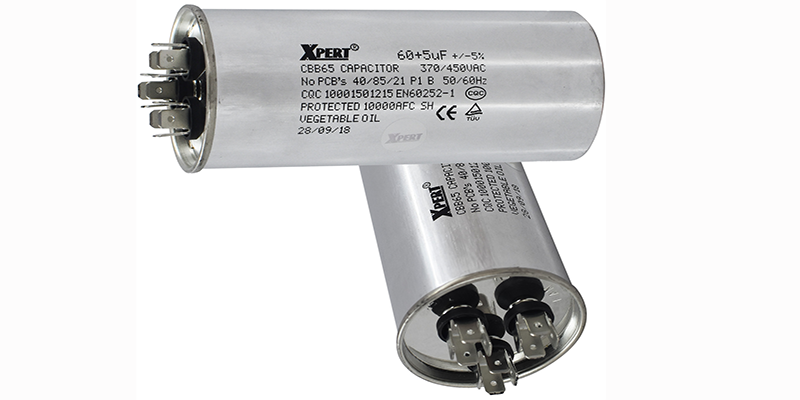
Power Factor Correction Capacitors
Power factor correction capacitors are used to improve power factor in electrical systems. Power factor is a measure that indicates how effectively electrical power is used in a system. Ideally, the power factor should be equal to 1, indicating optimal use of power. However, in practice, due to the presence of reactive loads such as inductors and capacitors, the power factor is usually less than 1, leading to lagging current or insufficient voltage conduction, and hence phase difference. This phase difference is what we recognize as power factor.
Power factor correction capacitors work by storing an electrical load for future use, aiding in smoothing out currents and reducing peaks and dips. They also assist in correcting lagging (inductive) or leading (capacitive) currents, thereby reducing the phase difference between current and voltage. This leads to an improvement in power factor.
Choosing the right power factor correction capacitor entails considering various factors, including the voltage and frequency of the system, the required level of power factor correction, the responsiveness and variability of the load, and potential harmonic levels in the system. Engineers often use the reactive power (Q) required for correction, measured in Volt-Ampere Reactive (VAR), to determine the correct capacitor rating. Additionally, the capacitor must have a nominal voltage higher than the peak voltage of the system to prevent damage.
While power factor correction capacitors offer numerous benefits such as reducing energy losses, minimizing costs associated with excessive power consumption, and improving the efficiency and stability of power systems, they must be used with caution. Improper use or overcompensation can lead to exacerbated conditions, resulting in excessive currents and potential damage to system components. Ensuring proper sizing and installation of capacitors is essential for safe and effective operation.
Dry Power Factor Correction Capacitors: Concept, Functionality, Pros, and Cons
In the electrical industry, improving power quality and the efficiency of power distribution systems is of paramount importance. Dry power factor correction capacitors are recognized as one of the tools for power correction in electrical systems. These capacitors play a crucial role by improving power factor, reducing energy losses, and increasing system efficiency. In this article, we introduce, discuss the functionality, and examine the pros and cons of dry power factor correction capacitors.
Introduction to Dry Power Factor Correction Capacitors:
Dry power factor correction capacitors are a type of capacitor used to improve power factor in electrical systems. The power factor indicates the efficiency in transferring power between power sources and consumers. The primary goal of these capacitors is to increase the power factor to optimize the use of electrical power and reduce losses in the system.
Types:
There are two main types of dry power factor correction capacitors:
1. Fixed Capacitors: These capacitors provide a fixed amount of correction and operate permanently.
2. Automatic Capacitors: In this type, the correction level is adjusted based on changes in the load in the electrical system, and they have automatic functionality.
Functionality of Dry Power Factor Correction Capacitors:
Dry power factor correction capacitors work by storing an electrical load for future use. These capacitors help improve the power factor by smoothing out currents and reducing peaks and dips. Additionally, they assist in correcting lagging or leading currents, resulting in a reduction in phase difference between current and voltage. They can be categorized as follows:
[Here, you may want to list the categories as mentioned in the text, but it seems the text lacks specific categorization details.]
Power Factor Correction: Dry power factor correction capacitors help by storing an electrical load for future use, aiding in “smoothing out” currents and reducing peaks and dips. These capacitors assist in correcting lagging (inductive) or leading (capacitive) currents, thus reducing the phase difference between current and voltage.
Energy Loss Reduction: By improving the power factor, dry power factor correction capacitors significantly reduce energy losses and contribute to a more environmentally friendly energy system.
Enhanced Efficiency and Lifespan: By optimizing the power factor, these capacitors reduce the demand on the electrical system, leading to improved efficiency and lifespan.
Dry power factor correction capacitors play a crucial role in enhancing the power quality and efficiency of electrical systems by providing energy loss reduction and performance improvement. However, the optimal and proper use of these capacitors requires a precise understanding of their functionality and technical specifications to prevent potential issues in electrical systems.
Oil Power Factor Correction Capacitors:
Oil power factor correction capacitors are essential tools in improving the efficiency of power transmission and distribution systems. By correcting the power factor, which is the phase difference between voltage and current in an AC circuit, these capacitors contribute to enhancing power quality and efficiency in electrical systems. Here, we delve into the specifications, performance, and applications of oil power factor correction capacitors.
Specifications:
Structure and Material: Oil power factor correction capacitors are generally made of metallized polypropylene film. However, some of them also use metallized polyester film or paper. Dual metallized paper capacitors are typically used in applications requiring robust power factor correction solutions.
Harmonic Content and Transient Operations: These capacitors are designed to manage high harmonic content and transient-free operation. They are suitable for applications involving large inductive loads such as oil drilling rigs, wind turbines, large motors, and electric arc furnaces.
Performance:
The power factor correction mechanism in these capacitors is based on absorbing reactive power and correcting the ratio of active power to reactive power (power factor). By reducing the supply line from reactive power, these capacitors help improve the power factor. This is achieved by storing reversed magnetic energy, thereby compensating for lagging current and enhancing overall power factor.
Applications:
Industrial and Commercial Use: Oil power factor correction capacitors are widely used in various industries to correct the power factor, reduce reactive power, and increase electricity consumption efficiency by inductive loads. This leads to loss reduction, voltage improvement, system capacity enhancement, and reduced electricity bills.
Installation Options: These capacitors can be installed as standalone units for easy installation or replacement, or as capacitor banks for power substations or large facilities. Automatic switching systems can provide precise power factor correction capacitors, making them suitable for facilities with multiple loads and variable conditions.
Oil power factor correction capacitors play a crucial role in improving the efficiency of power transmission and distribution systems by correcting the power factor. With the ability to manage high harmonic content and provide benefits in terms of loss reduction and efficiency improvement, these capacitors have become an essential component in power factor correction systems.
Comparison of Dry and Oil Power Factor Correction Capacitors
In comparing dry and oil power factor correction capacitors, we can highlight key differences in their structure, performance, and environmental impacts. This comparison aims to provide a comprehensive and accurate perspective on the characteristics of each type of capacitor:
Impregnation and Partial Discharge Voltage:
Oil Capacitors: They use a saturating liquid for impregnation, replacing air voids on the surface, and have a higher partial discharge voltage.
Dry Capacitors: These capacitors are not impregnated with oil and have a lower partial discharge voltage.
Hermetic Sealing:
Oil Capacitors: They are hermetically sealed to prevent exposure to weather conditions.
Dry Capacitors: This type of capacitors is usually not hermetically sealed and may be affected by the environment.
Structure and Durability:
Oil Capacitors: Their wound elements are enclosed in metal containers with sufficient thickness and hermetically sealed with wax. This structure leads to greater durability and stability.
Dry Capacitors: They typically have a simpler structure compared to oil capacitors, resulting in less durability.
Cooling and Suitability for Tropical Conditions:
Oil Capacitors: The free flow of saturated materials inside the capacitor containers provides uniform cooling, making them highly suitable for tropical conditions.
Dry Capacitors: Compared to oil capacitors, dry capacitors are not suitable for tropical conditions, and their performance may be affected.
Dielectric Materials:
Oil Capacitors: They use specialized dielectric materials for impregnation that provide specific characteristics such as higher partial discharge voltage.
Dry Capacitors: Their dielectric materials are usually made of polypropylene or similar substances, and some of them also have self-healing properties.
Dielectric Losses:
Oil Capacitors: Their dielectric losses are usually lower than those of dry capacitors.
Dry Capacitors: This type of capacitors has low dielectric losses, which are crucial for maintaining efficiency in power systems.
Environmental and Safety Considerations:
Oil Capacitors: Due to the need for oil impregnation, issues such as oil leakage and potential environmental contamination may arise.
Dry Capacitors: They generally have fewer environmental and safety issues.
The choice between oil capacitors and dry capacitors depends on specific application requirements, environmental conditions, and cost considerations. Each type of capacitor has unique features and advantages that should be selected based on the specific needs of the system.
Read more: Power Factor and Reactive Power Compensation Solutions
Summary
Since capacitors play important roles in power factor correction and improving the performance of electrical systems, comparing dry and oil power factor correction capacitors has been of interest. Oil capacitors, with features such as high partial discharge voltage, hermetically sealed structure, and longer durability, have become a suitable option for conditions requiring greater stability. On the other hand, dry capacitors, with properties like lower dielectric losses and self-healing capabilities, have become a desirable choice for applications needing energy loss reduction and self-healing features.
Overall, the choice between these two types of capacitors should be based on the requirements, environmental conditions, and technical specifications of each electrical system. Additionally, since each type of capacitor has its own specific features and advantages, the optimal choice may vary for each system. For example, in conditions requiring greater stability and longer durability, the use of oil capacitors is recommended, while in cases where energy loss reduction and self-healing properties are needed, dry capacitors will be the best option. Therefore, a precise understanding of the characteristics and requirements of the electrical system helps in making a more optimal choice between these two types of capacitors.
Read more: Introduction to Medium Voltage Capacitor and Its Applications